IV Line & Medication Label System
Do IV Line and Medication Labels really impact compliance, patient safety, make nurses jobs easier and reduce hospital costs? They do when they are standardized and optimized throughout the operation.
Executive Summary
This leading pediatric hospital is ranked among the top 10 children's hospitals in the country by U.S. News & World Report. With over 300 beds, they treat more than 200,000 children from the U.S. and around the world. However, this world class healthcare provider confronted compliance and risk management challenges.
In addition, like most hospitals, they wanted productivity improvements and cost reductions. So, they turned to RRD for a solution that:
- Exceeded Joint Commission (TJC) compliance and internal protocol requirements
- Improved patient safety
- Reduced SKUs
- Controlled costs
Essential Protocols And TJC Requirements
How do you provide dozens of patient care services and more than 500 patients each day while maintaining TJC requirements and meeting internal protocols? With over 1,700 nurses, it's not easy. But the challenge is more complex when IV Line and Medication Label colors, construction, formats and usage differ throughout the hospital. For example:
- The drug labels line identification lacked consistency
- Label formats differ throughout the hospital creating confusion among nurses
- The confusing formats caused inaccurate data input
- The confusing formats sometimes resulted no data input or blank lines
- When lines were left blank it created a possible TJC violation
A Collaborative Solution
The Medical Center partnered with RRD to develop a plan that consolidated the needs of risk management, nurses and patients. Working with Value Analysis and the other departments, RRD analyzed 150 unique line and medication labels used throughout the facility. They identified the various lines used on each label and the data input each one required.
For example, the date line on a simple “change minder” label had various meanings to different nurses. To illustrate, even though the day of the week, which indicates when the change should take place, is preprinted on the label, they assumed the date was also required. A redesigned label containing fewer lines and more descriptive wording cleared up the confusion.
The team looked for consistent processes. But, when they found a line that was represented inconsistently, like the change minder label, they noted the difference.
Armed with this information, they interviewed nurses in multiple departments to determine how they used the labels.
In addition, questions such as:
- Which lines were needed or not needed?
- How are date and time identified?
- Do you use an ASTM color system?
Program Results
The collaborative effort resulted in improved processes that exceeded TJC and internal protocols. Plus, the new system met Department Of Health requirements. In addition,
- Line and medication labels were standardized across departments including OR
- The label standardization process eliminated data input confusion
- Nurses no longer left lines blank!
But the results weren't exclusive to Risk Management and nursing. Supply chain benefited as well:
- SKUs were reduced by nearly 30%
- Although size, construction, the amount of colors and more increased, overall costs did not
Summary
RRD developed and implemented an IV Line and Medication label system that made nurses jobs easier while increasing compliance and improving patient safety. In addition, the total amount of unique labels required by the Medical Center decreased. And even with label material and design improvements, costs remained in check.
In addition, based on the program's success, they will use the same assessment process to evaluate and improve the anesthesia label category.
United Ad Label provides stock and custom label IV Line and Medication label products. Click here to review our stock items. Or contact us to learn how our solutions improve compliance and patient safety.
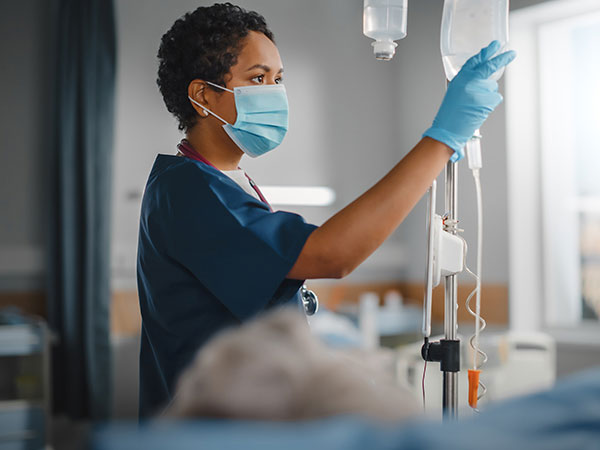