Biomedical & Clinical Engineering Label Tips
These biomedical and clinical engineering label tips are simple steps you can take.
- When manually applying a label to any surface, start by pulling the liner from the face sheet. By pulling the liner first, it will reduce the possibility of curl and better adhere to the surface.
- Storing labels in a climate controlled room is essential to best performance. For example, long term exposure to excessive heat and humidity or the cold and dry conditions typical of a warehouse setting throughout the year, will make the label more susceptible to failure. Common problems include curling and adhesive ooze. Plus, most label materials perform optimally for up to 1 year when stored at recommended environmental conditions of 72 degrees F and 50% relative humidity.
- When reviewing descriptions of labels to purchase, the dimensions are typically stated in Width (W) in inches x Depth (D) in inches. For example, the United Ad Label Equipment Inspection label is 1 ¼” x 1” or 1 ¼” wide and 1” deep.
- If you need a barcode label, use coated materials to increase barcode read rates. Although uncoated materials are generally less expensive, read rates are lower.
- If you conduct a test for scanability, use the same combination of label, ribbon/toner and scanner that you will use during the actual job. This process will ensure the most accurate results.
- Fun fact - Vinyl face sheets may smell like a new shower curtain!
- Vinyl face sheets for laser printing require top coating. United Ad Label press-applied topcoats can reduce material costs by up to 10% over the top coatings applied by the actual material supplier.
- Semi gloss face sheets can be overcoated with varnish to give the appearance of a high gloss face sheet at lower cost.
- Process color labels look best when printed on high gloss face sheets. But, if print quality is not critical, semi gloss and varnish are more cost effective options.
- If you are unsure that a label will stick to a surface, adhesion testing is critical! Whenever possible, test all materials on the surface for 24 hours under actual end use conditions.
- The time it takes for an adhesive to achieve full bond strength varies by adhesive type. Always allow test labels to "set" for at least 24 hours.
- Permanent adhesive will tear or pull fiber when removal is attempted from notebook paper after the adhesive has been allowed to "set."
- Removable" has many meanings. Clarify the time between application and removal, and if "no residue" is required. Test removability in the same way you test permanence. Always allow the test label to “set” for at least 24 hours before removing.
- If you need a full tint on your label, matte litho materials give you better ink coverage than uncoated EDP face sheets.
- Most thermal printers require 1/8” minimum spacing between the labels, and/or a timing mark on the back of the liner.
Helpful Label Information
Do you know the various components that make up a label? This label information will help you better understand how labels are constructed. And, it will help you make more informed, accurate and cost effective purchases.
- Facestock - Any paper or materials including films, fabrics, and foils that can be converted and used to produce the top layer of a basic label construction.
- Liner - The bottom layer in a pressure sensitive construction. The liner always has a release coating that prevents the adhesive from sticking permanently to the backing, which allows the face material and adhesive to be removed together when a label is being applied to a substrate.
- Substrate - refers to the surface onto which a label is applied.
- Permanent Adhesive - An adhesive which has high ultimate adhesion, which usually cannot be removed intact or only with enough force to overcome the adhesive bond – in which case the label may be damaged.
- Removable Adhesive - An adhesive with a low ultimate adhesion to a range of surfaces which can generally be removed or peeled-off intact.
- Repositionable Adhesive - An adhesive which enables a pressure-sensitive label to be removed and repositioned shortly after application.
- Gloss - A type of finish that yields a bright and shiny surface or colors
- Matte - A coated stock that’s not as shiny as a gloss finish but still has excellent print characteristics
Common Label Material Definitions
These are common label material definitions specific to biomedical and clinical engineering operations. If you are not sure what a term means, this is an excellent reference tool. You’ll often see these terms used to describe products you may use.
- Blockout - Often used to cover up dated information or mistakes, available with permanent adhesive but it is not tamper proof and is for indoor use only.
- Clear Film - A transparent gloss or matte label material used in applications where a “no-label” look is required. Not suitable for harsh environments because of its sensitivity to solvents. Fluorescent - Matte paper with an attention-getting bright colored facestock
- Freezer/Cold Temperature Applications - These materials are for use when the label is being applied in a cold temperature environment such as a freezer or an unheated warehouse.
- High Initial Tack - Aggressive adhesives that exhibit a strong initial bond when applied.
- Moderate Tack - Label adhesives that exhibit a moderate initial bond when applied. These materials may be short term repositionable, building stronger adhesion over time.
- Short Term Repositionable - These materials may be removed from a substrate and reapplied within a short period after initial adhesion.
- UV Resistance - Look for this feature when creating labels that will be exposed outdoors.
- Not for Small Diameter Surfaces - These materials have failed and should be avoided on substrates with small diameters such as test tubes and vials.
- Small Diameter Surfaces - These materials have been proven successful on small diameter substrates such as test tubes and vials.
- May be Glove Safe-Must - These materials are acceptable for applications requiring the use of latex gloves. The adhesive should be removed without tearing the gloves.
- Self-Laminating - This construction is typically used with handwritten labels and includes an attached overlay that is applied to protect label and writing from cleansers, oils and abrasion.
Label Material Selection Process
United Ad Label uses this same basic process to develop the labels for Biomedical and Clinical Engineering functions. However, you can use the same steps to determine the best fit material for your operation.
STEP 1. Identify the Print Technology/Printer (IF APPLICABLE)
The first step in properly identifying the label material to use for your application is to identify the
type of printer that will be used. Printer types include dot matrix, direct thermal, thermal transfer,
cut sheet laser, continuous laser, and ink-jet. Label materials are often modified for specific print
technologies.
STEP 2. Identify the Required Facesheet
There are a wide variety of face sheets available, each with specific performance characteristics. The
requirements of the application will dictate which facesheet to use. Paper facesheets are generally less
expensive and are the best choice for indoor/dry locations or short-term use. Performance of paper
facesheets can be changed by things like top coating or latex impregnation. Synthetic films will often
be required for durable product applications, or those with exposure to moisture, abrasion, chemicals,
or other contaminants. Film options available include polystyrene, polypropylene, vinyl, polyester, and
others. Performance enhancers like topcoats and other surface treatments are common.
STEP 3. Identify the Substrate
"Substrate" is the technical term for the product/material that a label will be applied to. Examples
include metal, plastic, corrugated, fiber drums, packaging films, etc. It’s also common that a labeling
application needs to work on more than one substrate. It’s key to obtain SPECIFIC substrate information,
especially for plastic as there are many different types. It is important to determine the entire
process, starting from the moment the label is applied, and ending when it has completed its useful life
cycle.
STEP 4. Identify the Required Adhesive Type
Repositionable adhesives are intended to be removed from the initial substrate/product and then
re-applied to the same product/substrate or a different product/substrate. It is important to verify the
length of time between initial application and re-positioning. Short-term repositionable means that the
time interval between initial application and re-positioning is short, the typical example being
immediate repositioning to straighten misapplied labels. Long-term repositionability requires special
adhesives that are "ultra-removable/ultra-repositionable."
STEP 5. Identify the Required Liner
Although the release liner is typically considered a "throw-away" part of a label, it is integral to the
overall label performance. The application will dictate the liner selection. 50# liners are good for fan
folding and are the standard for dot matrix printing which typically requires refolding. 40# liners are
the standard for roll labels primarily because the lower caliper allows more labels per roll.
STEP 6. Identify Other Application Requirements
Although many label applications are straightforward, others have unique usage requirements that can
affect material selection. Some examples of these unique usage requirements include: Permanent adhesives
that are intended to be adhered to a specific product/substrate and remain affixed for the lifespan of
that product/substrate. Are compliance requirements necessary?
- Are barcodes being printed on the label? (Barcodes require special considerations to ensure that they can be scanned effectively).
- Is this a Healthcare application? (Healthcare applications include special materials for IR scanning, for small diameter surfaces, for "glove-safe" use, etc.)
- If the label needs to cover up existing information a "block-out" adhesive may be required.
- Does the label need to be extremely durable? If yes, an overlamination may be required.
- Are there any other unusual processing or handling issues?
- Is the label exposed to extreme temperatures? If so, special materials are available to handle these conditions.
United Ad Label provides Biomedical and Clinical Engineering labels that are designed to withstand the rigors of healthcare applications. In addition, if you need a custom label and need assistance, contact our customer service staff for assistance.
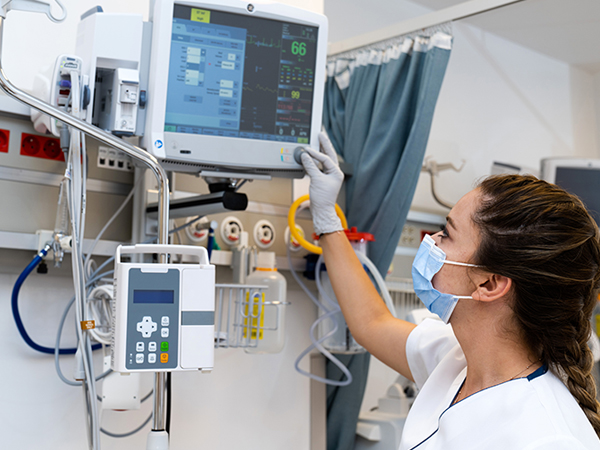