What’s worse than an internet outage? With so many connections to online applications, a disruption can prevent a wide range of activities, from transacting an online order to completing a simple task on the to-do list. But an internet outage isn’t the only problem causing wide-ranging impacts. Supply chain disruptions have created their own array of issues. And if your business uses labels to mark or ship products, guide medication dispensing, comply with safety regulations, monitor inventory and more, label material supply chain challenges may cause even more significant issues.
What Happens When Your Label Is Out Of Stock?
Regardless of your business, when you stock out of a crucial label, it puts your business at risk. Although our reliance on labels is less than the internet, an outage creates similar problems. From the inability to generate revenue because you are unable to ship finished goods to adding unnecessary risk to the medication administration process, a label is an essential supply for many organizations. Stock outs are simply unacceptable.
What Is Causing Label Material Supply Chain Disruptions?
As you would expect with the complexities inherent in any logistical process, numerous factors contributed to the label material supply chain disruptions.
Similar to automobiles, building materials and other industries that you see discussed more frequently in the news, the pandemic further exacerbated a tight label material supply. But one additional issue limited the amount of available production capacity. Only two of the top 10 worldwide paper companies are located in North America. With demand declining for printing papers over the past decade, consolidation became the method used to increase scale and reduce costs. During this process, many paper making machines were converted to produce different materials like paperboard and packaging or taken offline and not replaced. Because of the significant capital expenditures required for new production lines and questions over future material demand, companies were less willing to make capital investments in these slower growth segments. This resulted in an overall decline in North American fine paper production capacity. Even with demand increasing, lead times to add new production lines are lengthy so if new capacity is added, it won’t impact label material supply challenges in the short term.
In addition, during the pandemic, plant closings and temporary cutbacks in the workforce caused further disruptions. And then when plants reopened, not all employees were quick to come back, further slowing a return to normal production schedules.
Further setbacks came from multiple hurricanes hitting the Gulf Coast where many resins and adhesives used in label manufacturing are produced.
More recently, employees at the fourth largest printing paper company worldwide, UPM, located in Finland, went on strike on January 1, 2022. The work stoppage, which lasted nearly four months, had a significant impact on supplies. UPM is the leading supplier of face stocks and liner materials (label face stocks are peeled from the liner). Although UPM is located in Europe, there is significant demand for their products in the U.S.
Moreover, shipping challenges caused by delays in both Asian and U.S. ports, the Suez Canal blockage, and a shortage of truckers to transport those items to the end destination once the cargo ships did land, further slowed the supply chain and remain problematic today. Although those conditions are improving, it is still slowing the movement of raw materials necessary to produce the finished product.
But that’s not all. These supply chain challenges aren’t limited to label materials. For example, certain types of specialty inks and varnishes are in tight supply and so are items used to produce, package and ship labels including cores, cartons, shrink wrap, plastic bags, stretch wrap, banding material, pallets and more.
Learn how UAL worked with one customer to identify, test and supply and alternative material that allowed them to keep their operation running smoothly.
How Are Label Material Manufacturers Managing Supply Chain Challenges?
Label material manufacturers have implemented a few steps to manage the supply chain challenges they face.
For example, facilities disrupted by strikes, limiting the availability of certain key materials, are identifying alternate materials that can potentially serve as an acceptable substitute. This includes working with converters like UAL to test materials in the production environment and with end users to ensure the material performs as needed.
Also, in an attempt to keep material flowing for existing applications, material suppliers have allocated materials to companies that purchased them previously and minimized or eliminated sales to new customers. Unfortunately, with raw materials in short supply this has led to extended lead times. Lastly, as you might expect when demand increases and supplies are tight, material costs have increased.
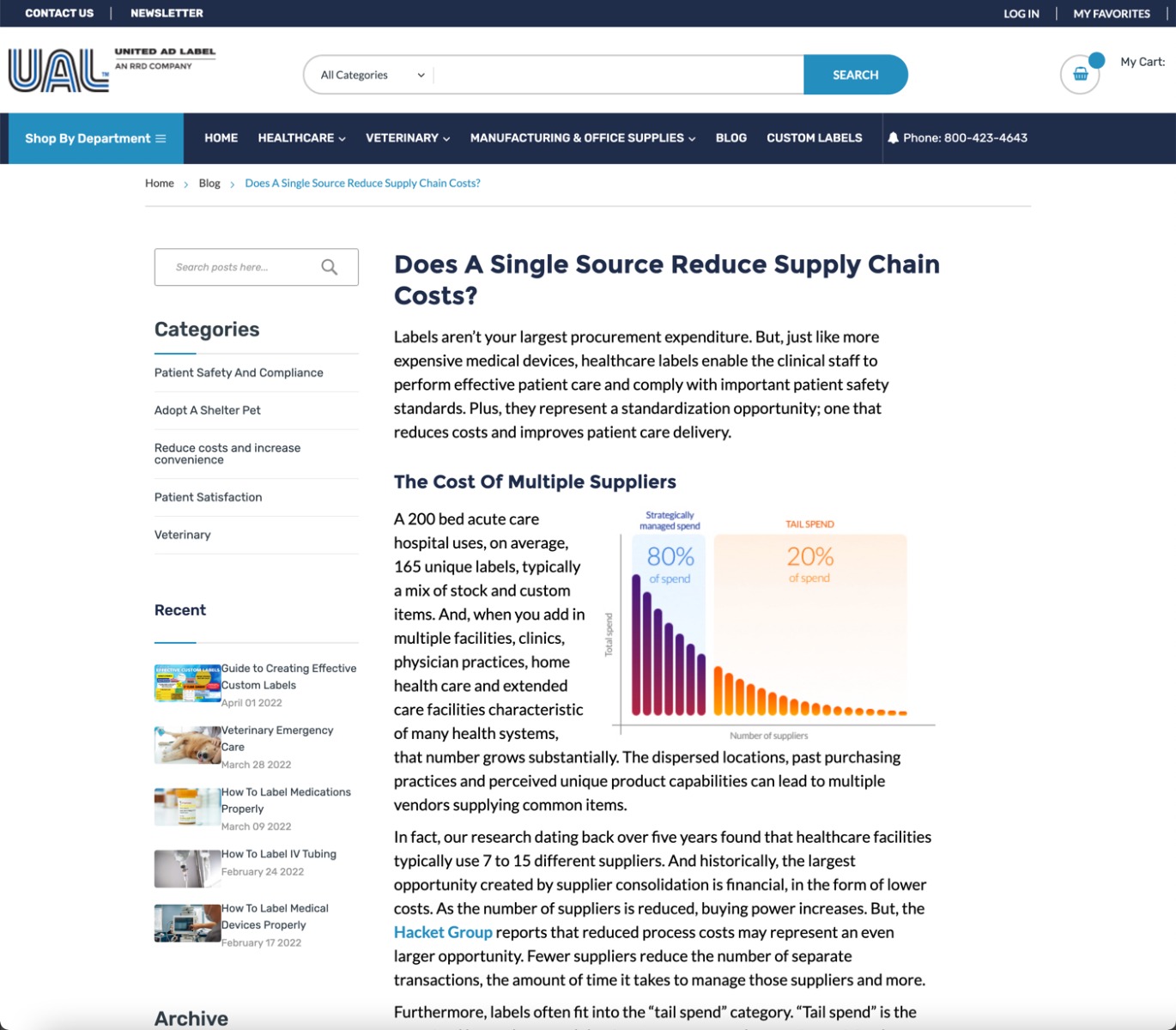
How To Manage Label Material Supply Chain Challenges?
The strain on label material supplies is not likely to abate quickly. So, it’s important to take steps like these to prevent outages and a negative impact on your business.
- Consider Alternatives - work with your label supplier to test alternative materials. For example, UAL is currently testing numerous materials from different sources to determine if there are viable alternatives to propose to customers in the case of material delays or outages.
- Plan Ahead - same day and next day deliveries, sometimes for little or no additional cost, have conditioned us to expect similar outcomes for all shipments. But, that’s no longer the case. Build in additional lead times in case of temporary stock outages or shipping delays. Plus, avoiding an emergency next day shipment will eliminate an unnecessary expense.
- Order Larger Quantities - instead of your normal order quantity, consider increasing it. In addition to ensuring you have stock on hand, ordering in larger quantities may provide an overall reduced cost when you consider all factors including the product, freight, purchase order creation, invoice payment and more. Although it’s difficult to know when supply chains will return to 2019 levels, it will eventually occur. When they do, you can make adjustments accordingly.
- Custom Storage - if you regularly order custom products a custom storage program allows you to order several months of those items, maintained in the suppliers warehouse. You can also preschedule shipments as necessary. This type of program reduces the label unit cost and saves on freight.
- Qualify Backup Sources - although suppliers throughout the industry are experiencing similar problems, a different provider may have options your current supplier doesn’t. At UAL we leverage the purchasing power of our parent company, RRD, which affords us access to material supplies that may not be available to other suppliers.
Learn more about United Ad Labels ready stock supply programs that help ensure product availability.
United Ad Label
In our 60 years in business, we’ve experienced supply chain challenges of all kinds. Through each one we’ve helped our customers avoid label supply shortages and get the products they need to operate their business. Please contact us to learn more about the steps we’re taking to minimize the impact of input costs and ensure you maintain a continuity of supply.